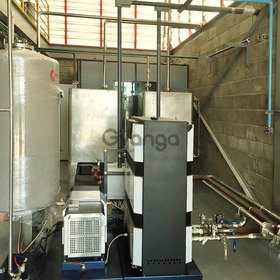
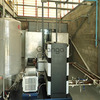
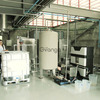
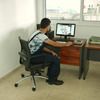
- 112 313.28 $ (USD)
- 9 367 210.88 ₹ (INR)
- 105 000 €
- 6 474 406.96 ₱
- 1.7722
(BTC)
- 34.6724
(ETH)
- 112 313.28
(USDT)
- 800.1231
(SOL)
- 2 109 256.72 R
- 4 153 729.11 ฿ (THB)
- 89 958.56 £
- 574 628.47 R$
- 412 515.44 د.إ
- 153 661.41 C$
- 1 927 307.30 $ (MXN)
- 421 225.36 ﷼
- 171 890.53 A$
- 4 458 380.22 UAH
- 10 351 450.82 RUB
- 189 111.52 $ (NZD)
- 6 600 363.03 RD$ (DOP)
- 445 348 139.05 $ (COP)
- 1 223 010.67 kr (SEK)
- 879 227.59 元
- 102 752.95 ₣
- 1 239 803.77 kr (NOK)
- 429 632.87 ₪
- 98 182 743.95 $ (ARS)
- 49 847 721.60 KZT
- 106 514 566.74 $ (CLP)
- 813 777.07 圓
- 368 461.78 BYR
- 17 756 174.98 円
- 56 442 337.26 ₡ (CRC)
- 30 329 117 142.86 Bs (VEF)
- Ad type: Offering
- Contact person: Artem
- Country: USA
- City: New York City (New York)
- Address: +380507383348 ватсап вайбер телеграм
- Phone Number: Show Number
- Please inform the advertiser that you found this ad on GVANGA.COM
- Ask a Question
EQUIPMENT FOR BIODIESEL PRODUCTION
from any Vegetable oil - sunflower, rapeseed, cottonseed, coconut, etc.
Unlike companies that produce equipment for the production of biodiesel, based on old, “barrel” technologies used more than a century ago, our company uses the principle of magnetic pulse high-frequency cavitation, used in secret technologies, allowing us to achieve significant advantages:
Undemanding to the quality of the source oil
High-frequency magnetic-pulse cavitation reactors operate successfully and stably on both raw and refined oil, as well as all types of animal fats and their mixtures with vegetable oils. These are sunflower, rapeseed, flaxseed, palm, mustard, etc., with almost any acid number, as well as waste of overcooked oil from restaurants and bakeries, beef, pork and chicken fats - waste from livestock and poultry processing factories. In this case, no re-adjustment of equipment is required when changing the type of oil.
Completion of the reaction “in one pass”
In magnetic pulse cavitation technology, it is not necessary to carry out a repeated transesterification reaction, as in the old “barrel” technologies. The time to obtain finished biodiesel is reduced by 8-10 times.
No cleaning with sorbents, washing or drying of biodiesel is required.
In traditional technologies it is impossible to immediately obtain biodiesel of proper quality. Therefore, they are forced to wash it or use sorbents to remove all impurities. This requires additional equipment for washing primary biodiesel (for this, a mixture of water and alcohol is usually used) and an additional installation, the so-called vacuum drying. With the cavitation method of producing biodiesel, neither washing nor drying of the final product is required; therefore, there is no need to dispose of used water or sorbent.
Minimal amount of alcohol and catalyst. No alcohol recovery.
One of the serious problems of “barrel” technologies is the need to add excess methanol to the reactor and, accordingly, its subsequent distillation (recovery). This requires the installation of additional equipment and energy costs. In cavitation technologies, the amount of alcohol used in the reaction exactly corresponds to the stoichiometric composition, i.e. minimum volume. There is no need to repeat the transesterification reaction. Expensive and dangerous methanol stripping equipment is eliminated. The inevitable loss of alcohol during recovery is eliminated, the environmental situation and explosion safety are improved.
Minimum energy consumption
Traditional methods for producing biodiesel are based on heating the oil to 65-70° C. This requires significant energy consumption, in addition, the recovery of excess methanol (a necessary condition for the reaction in traditional technologies), additional transesterification, as well as vacuum drying leads to significant energy consumption. With cavitation treatment, all this is not required, and as a result, energy savings are 5-7 times.
Low-temperature reaction
Magnetic-pulse high-frequency cavitation treatment in the reactor occurs at the molecular level. All components are exposed to pulses of magnetically directed cavitation. Fatty acid molecules rupture through microexplosions; this leads to a decrease in viscosity, an increase in the cetane number, an improvement in the energy characteristics of the future fuel, and also significantly increases the speed and quality of the esterification reaction. In this case, the reaction takes place at room temperature. There is no need to heat the oil.
Minimum overall dimensions of modules
Our automatic modules take up 5-10 times less space than traditional complexes of similar performance.
Biodiesel from vegetable oil.
Installation BNR 1000 (1000 liters per hour) automatic
The BNR 1000 automatic system consists of:
PPS-CT 1200: electronic system for pre-dosing and processing of raw materials.
ROTON-B 30 - magnetic pulse reactor for BNR 1000. magnetic pulse reactor
Automatic control system (electrical cabinet, PLC, PC, software, etc.)
Pipes, fittings, etc.
Separation system:
6.1. Separation tank, sensors, pump, valves, etc.
7.2. Electronic monitoring system for filling, separating and unloading finished products
Technical specifications:
Productivity, liter per hour
1000-1200
Rated power, kW
33
Weight (approx.), kg
985
Degree of automation
full
Operating mode
continuous
Processing capacity, kW hour / liter (no more)
0.028
Capacity adjustment
Yes
Area occupied by one module, m2
3.5
Overall dimensions (L x W x H), mm
2870x1390x2620
The CTS company has developed new modules for the production of BioST biodiesel based on the new PULSAR - CT 730 cavitation reactors . Eleven standard sizes of BioST units allow you to process from one to sixteen cubic meters of oil in one hour (or more, if necessary).
A particularly precise dosing system based on the Coriolis principle, new generation cavitation reactors, a reliable separation system that has proven itself over the years of trouble-free operation, original software with a user-friendly interface - all this makes BioST the most efficient and modern equipment on the biodiesel production market.
For the production of BioST, we cooperate only with reliable and well-known global suppliers, such as Grundfos , Siemens , Schneider Electric , Moeller , Fanuc , etc.
Powerful BioST controllers monitor all parameters of the biodiesel production process, such as product consumption, reactor temperature, separation process, finished product yield, and also monitor the operation and condition of all mechanisms included in BioST . The operator just needs to enter data about the initial products into the computer and press the START button - BioST will do the rest .
All BioST mechanisms are ATEX certified , which ensures safe operation of the unit with liquids such as methanol and catalyst.
BioST operate in continuous mode and do not require operator intervention except in extraordinary cases. BioST will inform the operator of any error if one occurs during operation, and will provide brief recommendations on how to resolve the problem.
BioST keeps records of the consumption of raw materials and equipment operating time. BioST
units can process any type of vegetable oils and mixtures of various oils, as well as waste oils from restaurants, cafes, etc. Further processing of biodiesel obtained at BioST - washing, drying, methanol recovery - is not required. This makes it possible to significantly reduce the production time of finished biodiesel and reduce energy consumption compared to traditional outdated technologies. The level of BioST
automation has been brought to the maximum, which avoids the “human factor” and, as a result, significantly reduces possible operator errors. BioST can
be operated by an operator who has undergone basic technical training and has minimal computer knowledge. BioSTs are designed to operate continuously for 24 hours and require no special maintenance.
Browse all classified ads in category Industrial Equipment & Parts in New York